News
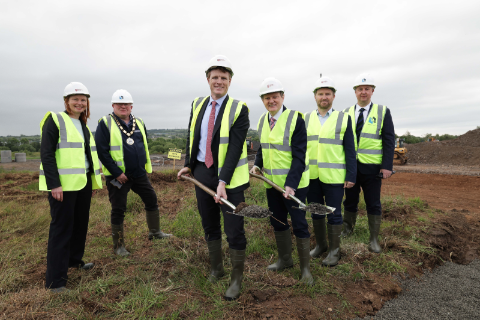
Construction starts on Factory of the Future to reinvigorate Northern Ireland’s industrial potential
12 June, 2024
Construction has started on a state-of-the-art Factory of the Future at Global Point in Newtownabbey led by Queen’s University Belfast, which is key to an exciting future for advanced manufacturing in Northern Ireland.
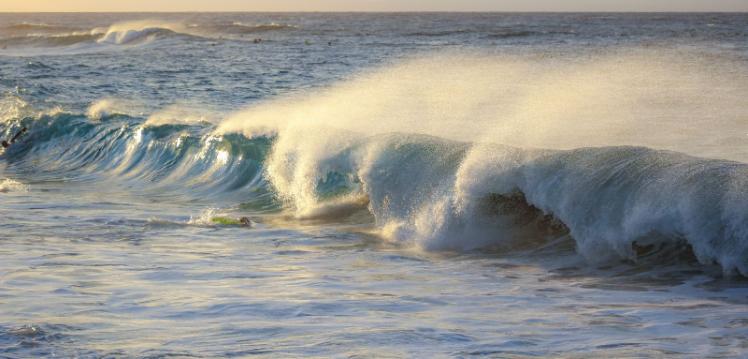
6 September, 2023
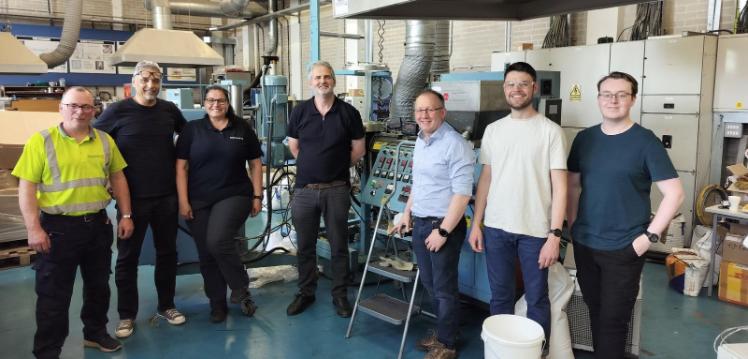
23 June, 2023
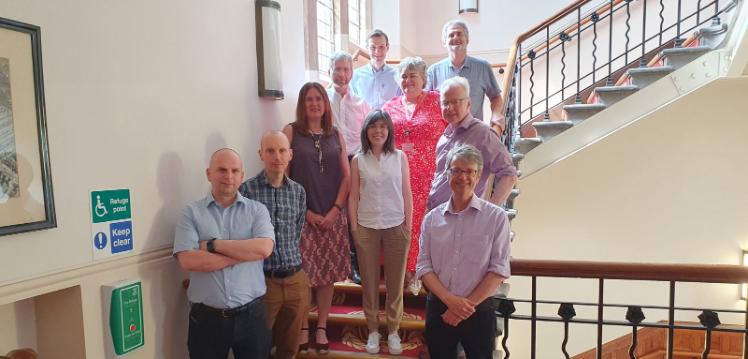
14 June, 2023
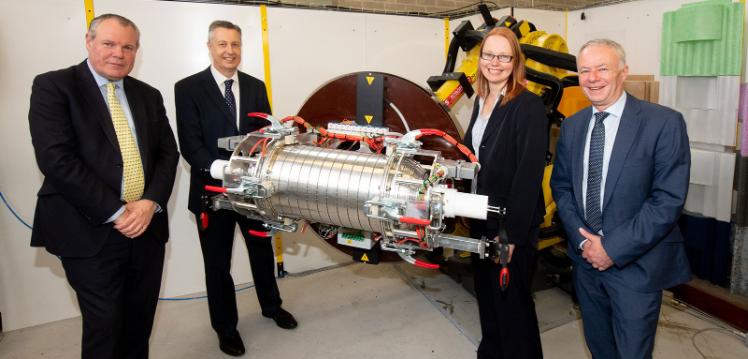
11 April, 2022
Minister of State for Northern Ireland Conor Burns has visited Queen’s University ahead of a two-day event which will bring together over 70 leaders in advanced manufacturing to shape the future of a £98m world-class facility for the industry.
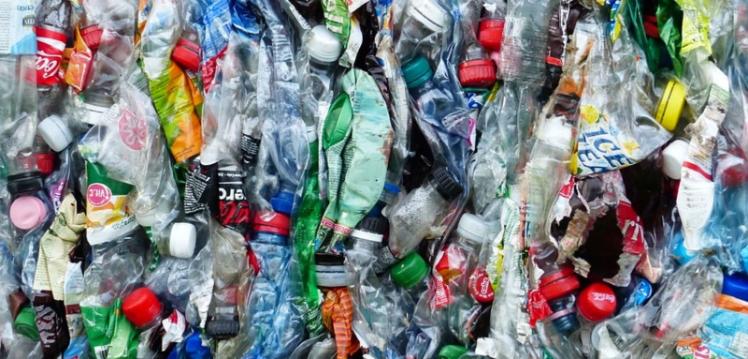
9 November, 2021
Researchers at Queen’s University Belfast have been interviewing people across the region to try to crack the puzzle of why some people recycle and others don’t.
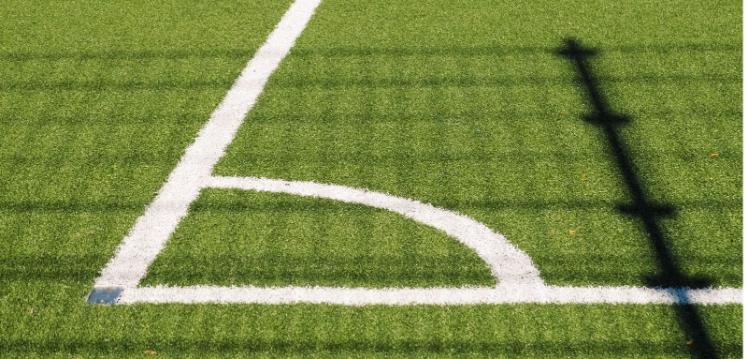
15 October, 2021
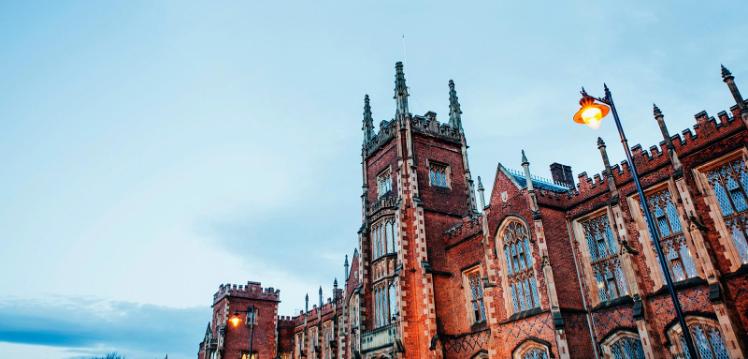
21 September, 2021