Dry Silicon Etching
Deep reactive-ion etching (DRIE) is a highly anisotropic etch process used to create deep penetration, steep-sided holes and trenches in wafers/substrates, typically with high aspect ratios. It was developed for microelectromechanical systems (MEMS),
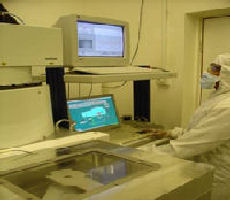
Dry silicon etching is carried out in an Alcatel i-speeder 100 system.
The system is capable of etching silicon using a standard BOSCH process switching between SF4 and C4F8.
A pure SF6 etch is typically used for back side etching.
An end point detector is incorporated into the system for precision.
The system is capable of processing up to 200mm substrates
The BOSCH process alternates repeatedly between two modes to achieve nearly vertical structures.
- A standard, nearly isotropic plasma etch. The plasma contains some ions, which attack the wafer from a nearly vertical direction. [SF6] is often used for silicon.
- Deposition of a chemically inert passivation layer. (For instance, C4F8)
Each phase lasts for several seconds. The passivation layer protects the entire substrate from further chemical attack and prevents further etching. However, during the etching phase, the directional ions that bombard the substrate attack the passivation layer at the bottom of the trench (but not along the sides). They collide with it and sputter it off, exposing the substrate to the chemical etchant.
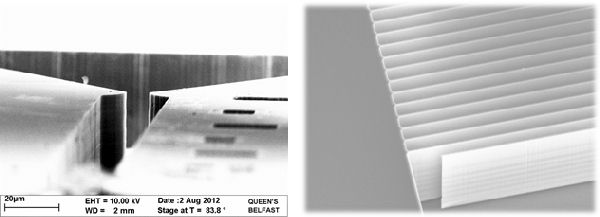
These etch/deposit steps are repeated many times over resulting in a large number of very small isotropic etch steps taking place only at the bottom of the etched pits. Creating the distinctive undulating or scalloped sidewall associated with the Bosch process. An etch process such as this will typically show an etch selectivity of 100 between silicon and silicon dioxide.
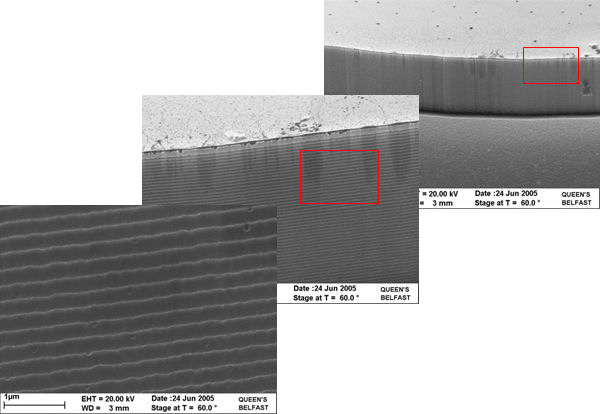
Slow silicon etching employing a BOSCH process with fast gas switching with low power and optimised process conditions BOSCH process produces vertical sidewalls with minimal scalloping
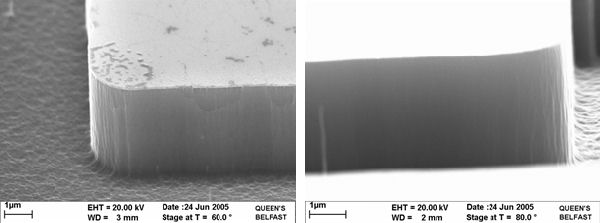
SF6 Blanket Silicon Etch
For bulk removal of silicon a purely SF6 etch is preferred. This yields a selectivity of over 1000 between the silicon and silicon dioxide removal rates. Allowing the thickness of the mask and the buried oxide stopping layer to be reduced. SF6 etching also produces a very smooth silicon surface after etch and requires none of the refinements to prevent grass formation. However there is significant lateral etching as can be seen from the micrographs of the bonded cavity structures below.
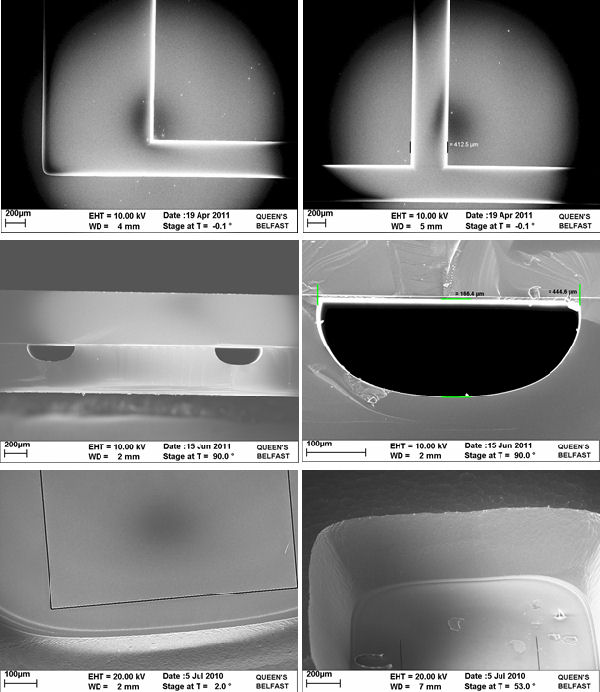
SF6 etching has been found to be particularly useful for back side etching or releasing structures defined into SOI. (µPAS presentation)