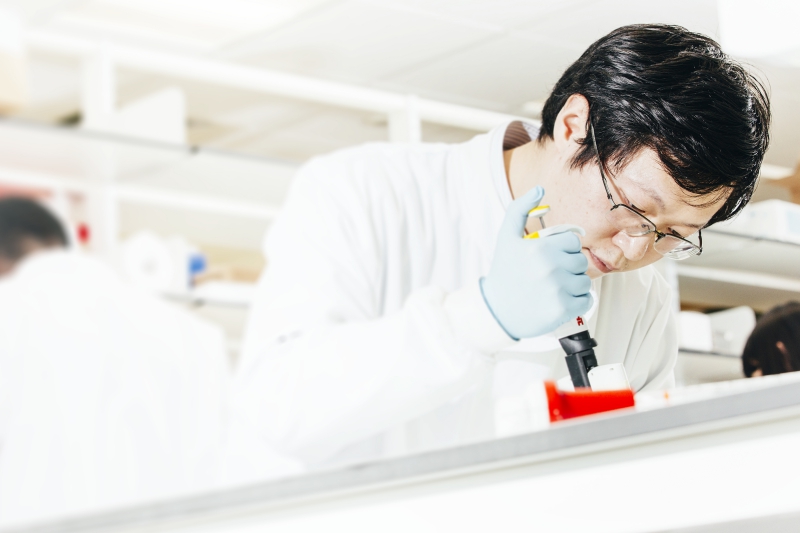
The University is committed to ensuring that exposure of employees and students to biological agents that are potentially hazardous to health is prevented or adequately controlled. This policy applied to all work activities involved in the handling, use, transport and storage of Biological Agents. The University's policy and procedures are based on the requirements of national legislation and extensive guidance produced by various expert technical advisory committees issued in support of the Regulations. COSHH defines a Biological Agent as a “micro-organism, cell culture, or human endoparasite, whether or not genetically modified, which may cause infection, allergy, toxicity or otherwise create a hazard to human health”.
Biological Safety Documents' Library-
BioCOSHH
The Control of Substances Hazardous to Health Regulations 2005 (COSHH) impose duties on the University to protect its staff and any other persons, whether at work or not, who may be affected by the hazards of the University's work involving substances hazardous to health, including biological agents.
A risk assessment must be undertaken prior to any work commencing to enable the employer to assess the risks involved and to adequately control the exposure of their employees to substances hazardous to health.
The Regulations also require that an assessment shall be reviewed regularly and forthwith if:
- There is reason to suspect that the assessment is no longer valid; or
- There has been a significant change in the work to which the assessment relates, and
- Where, as a result of the review, changes in the assessment are required that those changes be made.
The Safety Service provides templates for both chemical based COSHH assessments and biological based COSHH assessments, the latter being termed BioCOSHH assessments. GMO risk assessments also have their own templates.
Risk Assessment forms:
- Safety Committees
Biological and Infectious Agents' Advisory Committee (BIAAC)
BIAAC meets three times a year to discuss and advise on all aspects of biological and infectious agents safety work throughout the university. The committee oversees the work involving genetic manipulation and ensures all such work complies with guidance from the Health and Safety Executive Advisory Committee on Genetic Manipulation. A specialist sub-group of BIAAC review systematically and in detail, every risk assessment involving genetic modification. GMO risk assessments for review by the BIAAC GMO Sub-Group are submitted through the University Biological Safety Officer.
Health and Safety Management Group
The Health and Safety Management Group is responsible for making recommendations, through the University Operating Board, on policy and strategy relating to the management of health and safety, including:
- the development of policy and procedures;
- the structures and systems for the effective management of health and safety;
- the plans and objectives for continuous improvement;
- the resources for the achievement of plans and objectives;
- the monitoring of the implementation of policies and procedures;
- the development of health and safety training programmes;
- the review of health and safety performance and making recommendation for improvement to management.
Health and Safety Consultative Committee
This statutory committee provides the opportunity for employees to participate in the development of strategic health and safety policies for the University. Its purpose is to provide a forum for the formal consultation and communication with employee representatives on health, safety and welfare matters at work.
Local Safety Committees
Heads of School/Directors are responsible for ensuring that, within their School/Directorate, there is an effective health and safety forum for consultation with staff and students regarding health and safety at work. This may include creating a Safety Committee.
- Containment Laboratories
Work with biological materials, including microorganisms and genetically modified organisms, is undertaken in containment laboratories.
There are four different levels of containment (levels 1 – 4) for laboratory work, each containment level being directly related to each equivalent Hazard Group. Thus, organisms categorised as Hazard Group 1 (lowest hazard rating) should normally be handled in Laboratory Containment Level 1 facilities, and likewise up to Hazard Group 4 (highest hazard rating) in Containment Level Four facilities.
The vast majority of Queens University biological laboratories are Containment Level 2. There are also a small number of Containment Level 3 laboratories but none at Containment level 4.
The requirements of each laboratory containment level are made up of a combination of physical parameters and work practices. Details of the containment measures are defined by three similar, but separate systems of containment from:
- Local Biological Safety Officers
University Biological Safety Officer Dr David Norwood Patrick G. Johnston Centre for Cancer Research Dr Colin Adrain Wellcome Wolfson Institute for Experimental Medicine Professor Andriana Margariti School of Biological Sciences Dr Mark Robinson School of Pharmacy Dr James Burrows - Biological Safety Cabinets
Microbiological Safety Cabinets
A microbiological safety cabinet (MSC) is a ventilated enclosure intended to offer protection, to the user and the environment, from aerosols generated when handling biological agents or material that may contain such agents.
There are 3 main types of safety cabinet. The correct safety cabinet for your work depends on a number of factors:
Class I
This is the traditional cabinet of microbiology and clinical diagnostic laboratories. Its construction is simpler than the other types and is therefore cheaper to produce and buy. It works by drawing air into the cabinet away from the worker and then through a High Efficiency Particulate Air [HEPA] filter. It is the cabinet of choice when the key requirement is the protection of the worker.
Class II
These cabinets are designed so that the work area is kept clean by a down-flow of HEPA-filtered air across the work. With good working technique it is possible to achieve both a high degree of product protection and a operator protection of the same order as that provided by Class I cabinets. However, their performance is more affected by other factors, such as operator movement and air movements outside the cabinet. They are typically used for cell and tissue culture applications and for other work where product protection from contamination is important.
Class III
Class III cabinets are designed to completely contain the hazardous agent and are used mainly for work with hazard group 4 organisms or work with hazard group 3 organisms deemed to be at high risk, for example where highly concentrated samples are being handled. They offer the greatest protection to the worker and work, but movements are more restricted, and this may affect dexterity.
Laminar flow hoods
Laminar flow hoods should not be confused with MSCs! These hoods provide a filtered air-flow which is intended for product protection only. The cabinets must not be confused with Class II cabinets as they have no inflow, indeed the air passes over the product being worked on [e.g. cell culture] and so they offer no operator protection. Therefore, laminar flow hoods must not be used with any biological material of human origin. Other animal-derived material or tissue may only be used after a full risk assessment that confirms the total non-pathogenic and non-allergenic status of the material. They also must not be used when handling biological agents [pathogenic organisms].
Maintenance
Microbiological Safety Cabinets are maintained in compliance with COSHH regulations and ACDP guidance according to the schedule described in the table below. The servicing of Inflow/Down flow cabinet capability may be increased to 6-monthly for Class II cabinets in CL2 laboratories if required following risk assessment.
Test
Class I
Class II
Class III
Alarms/Indicators
Daily
Face Velocity/Inflow
Monthly
N/A
Inflow/Downflow
N/A
Annually for CL2,
6-monthly for CL3
6-monthly for CL3 and CL4
OPFT
Annually
N/A
In use OPFT
As required by assessment
N/A