Thomas Fisher
Mr
PhD Tom Fisher
Postgraduate Students
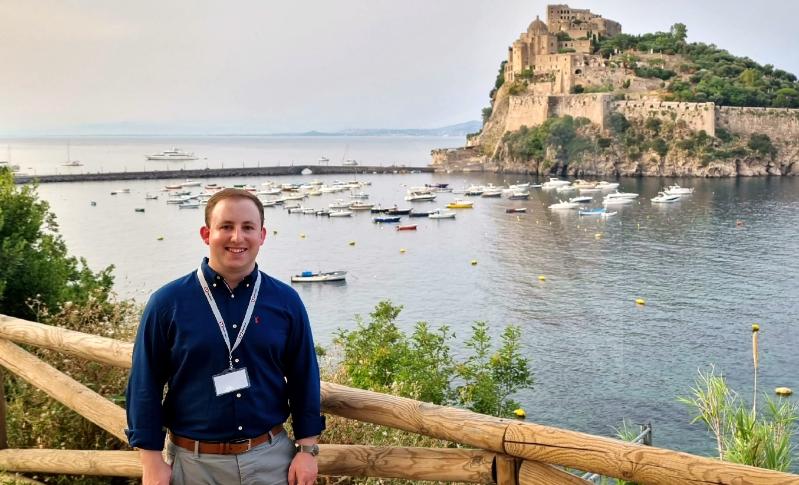
Tom graduated with an MEng from the University of Cambridge in 2018 where he focussed primarily on mechanical engineering and materials. His final year project, supervised by Dr Graham McShane, investigated the application of auxetic structures for impact protection. Following two years in the medical device industry, Tom joined ACRG in October 2020 to further his work in the fields of auxetics and impact. He is currently working on the development of a lightweight combat helmet using additively manufactured auxetic structures.
Email
Email